Waste Conversion Process
BMI ’s system combines existing commercial technologies with our patented front-end feedstock preparation technology to produce clean, renewable energy with minimal emission or disposal concerns. Our patented technologies ingest biogenic or carbon-based feedstocks (such as wood, municipal solid waste (MSW), agricultural waste, and other organic materials) to produce renewable diesel fuels and pure green hydrogen at costs below those of large-scale facilities. The reformation processes produce these fuels with significant reductions in greenhouse gas emissions compared to traditional refining processes.
​
The process can produce the following products:
-
Renewable Diesel
-
Sustainable Aviation Fuel
-
Green Hydrogen
-
Plastic Lumber (This requires additional equipment)
​
BMI is combining commercial technology in a unique way to enable consumption of all waste types. The technology “train” or “line” are 100 tons per day (TPD) continuously fed process and consists of:
The Patented Pre-Feed Process
The Pre-feed, which pre-blends or homogenizes the waste into a very specific moisture set point high-btu feedstock or “super” RDF ready for pyrolysis. The moisture vapor is removed collected from the incoming feedstock, condensed, and filtered into to R-1, R-2 water.

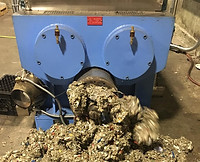
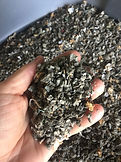
The Pyrolytic Conversion
Pyrolysis Technology takes the homogenized feedstock produced by the pre-feed technology, heats and cools it, and sends it to the patented Gas Enhancement Module (GEM) for final conversion to syngas. The GEM cleans and upgrades the syngas and begins the conversion to liquid transportation fuels.
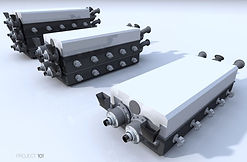


Fischer-Tropsch Process
Verdis Synthetic Fuels Fischer Tropsch Technology (Verdis FT Technology), a reactor in a shell-and-tube formation converts the syngas from the pyrolytic process into diesel or sustainable aviation fuels (SAF) through a separation and distillation process
